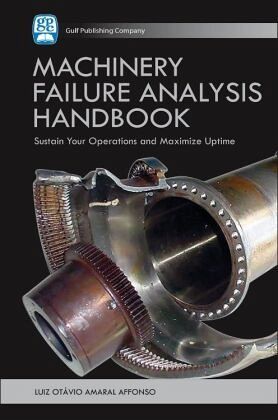
Machinery Failure Analysis Handbook
Sustain Your Operations and Maximize Uptime
PAYBACK Punkte
63 °P sammeln!
Understanding why and how failures occur is critical to failure prevention, as even the slightest breakdown can lead to catastrophic loss of life and asset as well as widespread pollution. This book helps anyone involved with machinery reliability, whether in the design of new plants or the maintenance and operation of existing ones, to understand why process equipment fails and thereby prevent similar failures.