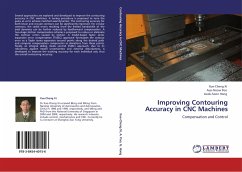
Improving Contouring Accuracy in CNC Machines
Compensation and Control
Versandkostenfrei!
Versandfertig in 6-10 Tagen
52,99 €
inkl. MwSt.
PAYBACK Punkte
26 °P sammeln!
Several approaches are explored and developed to improve the contouring accuracy in CNC machines. A tuning procedure is proposed to tune the gains so as to achieve matched axial dynamics. The contouring accuracy for both linear and circular contours can be significantly improved. For circular contours, the radial errors resulting from the limited bandwidth of the axial dynamics can be further reduced by feedforward compensation. A two-stage stiction compensation scheme is proposed to reduce or eliminate the contour errors caused by stiction. A model-based Taylor series expansion error compensa...
Several approaches are explored and developed to improve the contouring accuracy in CNC machines. A tuning procedure is proposed to tune the gains so as to achieve matched axial dynamics. The contouring accuracy for both linear and circular contours can be significantly improved. For circular contours, the radial errors resulting from the limited bandwidth of the axial dynamics can be further reduced by feedforward compensation. A two-stage stiction compensation scheme is proposed to reduce or eliminate the contour errors caused by stiction. A model-based Taylor series expansion error compensation (TSEEC) approach formulates the contour error as a Taylor series expansion around points along the desired path and compute compensation components as deviations from these points. Finally, an integral sliding mode control (ISMC) approach, due to its robustness against model uncertainties and external disturbances, is developed to improve the tracking accuracy for each individual axis, thus the overall contouring accuracy.